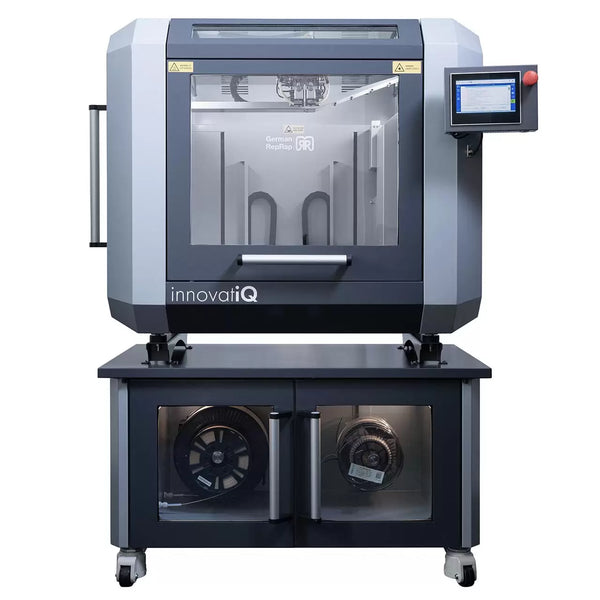
TiQ 5 – 3D printing for high-performance thermoplastics
The TiQ 5 is the optimal system solution for additive manufacturing of large functional parts. The unique SmartFunctions ensure intuitive and user-friendly use of the complex possibilities of additive manufacturing.
Equipped with a build space heater and a water-cooled dual print head, the TiQ 5 enables the process-reliable production of components made of a wide range of materials, especially high-performance thermoplastics. Whether for one-off production, large prototypes or industrial manufacturing – the TiQ 5 is always the right choice!
Features
Intuitive industrial control GestiQ Pro
The TiQ 5 is operated via the newly developed, intuitive GestiQ Pro industrial control system, which is located on a large tour display. all relevant functions of the printing system can be controlled with the help of a clear menu structure.
SmartStart: Fully Automatic System Leveling
Fully automatic system leveling makes labor-intensive adjustment of the print bed before each print job.
Water-cooled dual printhead
The TiQ 5 uses water-cooled DD4 dual extruder technology and is equipped with the new dual-lift extruders. The water-cooling ensures consistent precision of the printing process in continuous operation.
The print heads can be equipped with different nozzles, such as tungsten copper, depending on the application and material selection.
Nozzle replacement is user-friendly and can be carried out in just a few seconds, ensuring that even very special filaments, such as abrasive materials, can be processed without much effort.
Maintenance-friendly cooling concept
The TiQ 5 is equipped with the latest water cooling technology, which takes into account all temperature-sensitive electronic and mechanical components. These include the extruder and laser motors as well as the motors for the print bed leveling and filament feeding. The innovative cooling concept ensures high process reliability even when using materials with the highest processing temperature and a long printing time.
SmartTrack: Filament Feeder with Intelligent Tracking System
SmartTrack describes a sophisticated system consisting of the material feeder for automated material feeding and an intelligent tracking system. SmartTrack ensures a printing process with maximum process reliability by optimally coordinating material feed and printing speed.
SmartSpeed: Maximum print speed with the highest quality
Together with SmartTrack, SmartSpeed ensures that material feed and print speed are automated and coordinated during the printing process. While SmartTrack ensures optimum material feed, the print speed of the TiQ 5 is intelligently and dynamically controlled by the SmartSpeed process.
This is achieved by permanently measuring the filament feed in the print head. The industrial control system processes this measurement data using the SmartSpeed algorithm and dynamically adjusts the printer speed. With SmartSpeed, the printing process takes place in optimum quality at maximum printing speed.
Direct Drive material feed
The sophisticated automated material geed system ensures a self-contained and transition-free printing process that continues to work seamlessly even after a filament change.
Direct Drive ensures a printing process without interruption in the material supply. Flexible material in particular can be processed easily, as they leave the print head at the correct temperature and consistency without any offset. The system is Mae of hardened steel, so even processing abrasive materials is not a problem.
The system is optimized for a material diameter of 1.75 mm and thus ensures a high-level of process reliability during material feeding.
Specs
Extruders | water-cooled DD4 1.75 mm |
Extruder Temp (Max) | 400°C 752°F |
Resolution (max) | 20 microns 0.02 mm |
Accuracy | +/- 0.1 mm |
Heated Bed Temp (max) | 160°C 320°F |
Heated Chamber Temp (max) | 80°C 176°F |
Build Volume | 500 x 400 x 450 mm 19.7 x 15.7 x 17.7 in |
Speed (max) | 150 mm/s |
Materials | Open-Material Configuration, including PEKK-CF, PEI, Nylon (PA), PA-CF, PA-GF, Metal-Fill, ABS, PLA, PVA, PET, HiPS, TPU, Carbon20, Dupont Zytel (Nylon), DuPont Hytrel (Flexible), BASF Ultrafuse (Metal) |
Voltage | 230V European Standard |
Power | 2.3kW, 20-30% in continuous operation |
Weight | 408 lbs. |